As environmental awareness grows, establishing a 20t/h complete feed mill plant requires careful consideration of environmental protection measures. These investments are essential not only for regulatory compliance but also for promoting sustainable operations and fostering positive relationships with local communities. This article delves into the specific environmental protection investments necessary for a 20t/h complete feed mill plant.
Dust Collection and Filtration Systems
Dust generation is a primary environmental concern in feed mill operations. If not properly managed, dust can pose health risks and pollution. Investments in this area include:
- High-Efficiency Cyclone Dust Collectors: Installed at various points in the production line, particularly in grinding and mixing areas.
- Bag Filter Systems: These systems provide thorough dust removal, capturing fine particles that cyclone systems might miss.
- Dust Suppression Systems: Utilizing water mists or foam to control dust at transfer points and storage areas.
The cost of a comprehensive dust collection system for a 20t/h plant can range from $100,000 to $300,000, depending on complexity and efficiency.
Wastewater Treatment Facilities
Although feed mills typically produce minimal wastewater, proper treatment is crucial. Investments in this area include:
- Oil-Water Separators: To eliminate oils and fats from wastewater.
- Sedimentation Tanks: For removing solid particles from water.
- Biological Treatment Systems: To break down organic matter in the wastewater.
- Filtration Systems: For final polishing of treated water before discharge.
The cost of a wastewater treatment system for a 20t/h feed mill might range from $50,000 to $150,000.
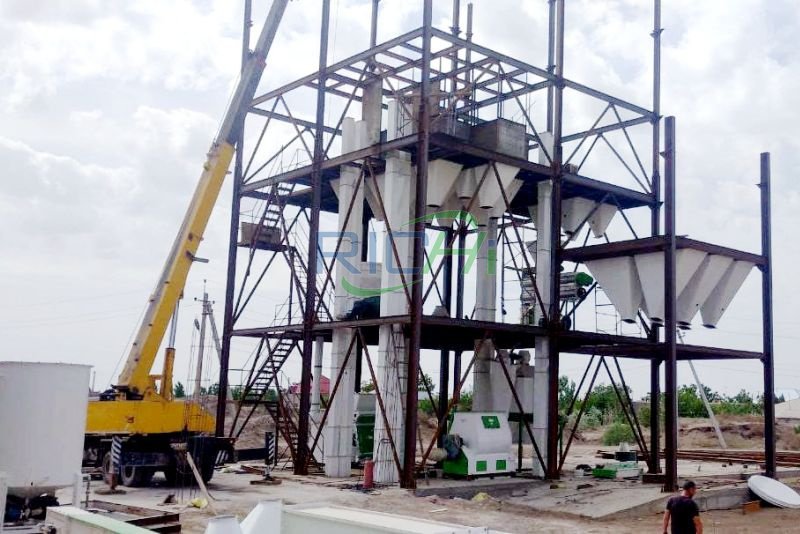
Noise Reduction Measures
Feed mill factory can produce considerable noise, which can disturb nearby residents. Investments in noise reduction include:
- Sound-Insulating Materials: For buildings and equipment enclosures.
- Vibration Dampeners: For machinery.
- Acoustic Barriers: Installed around outdoor equipment.
- Low-Noise Fans and Motors.
The cost for comprehensive noise reduction measures can range from $30,000 to $100,000.
Air Emission Control Systems
To manage gaseous emissions, particularly from boilers or dryers, investments may include:
- Scrubbers: For removing pollutants from exhaust gases.
- Low-NOx Burners: For boilers to minimize nitrogen oxide emissions.
- Catalytic Converters: To reduce harmful emissions from combustion processes.
Depending on specific requirements, air emission control systems can cost between $50,000 and $200,000.
Odor Control Systems
Feed mills can produce odors that may be offensive to nearby communities. Odor control investments might include:
- Biofilters: Utilizing microorganisms to break down odorous compounds.
- Chemical Scrubbers: To neutralize odorous gases.
- Ozone Treatment Systems: For oxidizing odorous compounds.
An effective odor control system might cost between $40,000 and $120,000.
Energy Efficiency Measures
While not directly related to pollution control, energy efficiency measures are crucial for minimizing the plant’s overall environmental impact. Investments may include:
- High-Efficiency Motors and Drives.
- Heat Recovery Systems.
- LED Lighting throughout the facility.
- Insulation Improvements for buildings and equipment.
Energy efficiency upgrades can cost between $50,000 and $200,000, often yielding significant long-term savings.
Solid Waste Management Systems
Proper handling and disposal of solid waste are essential. Investments in this area include:
- Waste Segregation Systems.
- Composting Facilities for organic waste.
- Compactors and Balers for recyclable materials.
- Secure Storage Areas for hazardous waste.
A comprehensive solid waste management system might cost between $20,000 and $80,000.
Spill Prevention and Containment Systems
To prevent contamination from spills of raw materials or finished products, investments include:
- Containment Berms: Around storage tanks.
- Impermeable Flooring: In storage and production areas.
- Spill Kits: Strategically placed throughout the facility.
- Underground Storage Tank Monitoring Systems.
These systems can cost between $30,000 and $100,000.
Environmental Monitoring Equipment
To ensure compliance with environmental regulations and promptly identify any issues, investments in monitoring equipment are necessary:
- Continuous Emission Monitoring Systems (CEMS) for air emissions.
- Water Quality Monitoring Equipment.
- Noise Level Meters.
- Particulate Matter Monitors.
A comprehensive environmental monitoring system can cost between $50,000 and $150,000.
Green Landscaping and Stormwater Management
Investing in the plant’s surroundings can help mitigate environmental impact:
- Retention Ponds: For stormwater management.
- Permeable Paving: To reduce runoff.
- Native Plant Landscaping: To support local ecosystems.
- Green Roofs or Solar Panels: On suitable buildings.
These landscaping and stormwater management features might cost between $30,000 and $100,000.
Environmental Management System (EMS) Implementation
Although not a physical investment, implementing an EMS is vital for ongoing environmental management:
- Development of Environmental Policies and Procedures.
- Staff Training on Environmental Practices.
- Regular Environmental Audits and Reporting Systems.
- Certification Costs (e.g., ISO 14001).
Implementing a comprehensive EMS might cost between $20,000 and $50,000.
Conclusion
The total investment for environmental protection in a 20t/h complete feed mill plant can range from $470,000 to $1,550,000, depending on specific requirements, local regulations, and technology levels implemented. Although this represents a significant upfront cost, these investments are crucial for several reasons:
- Regulatory Compliance: Many measures are legally required in most jurisdictions.
- Operational Efficiency: Many environmental protection measures enhance operational efficiency and reduce long-term costs.
- Community Relations: A commitment to environmental protection can improve relationships with local communities and stakeholders.
- Sustainability: These investments contribute to the long-term sustainability of the operation.
- Market Access: Increasingly, customers demand environmentally responsible production practices.
While these investments may appear substantial, they often lead to long-term cost savings through improved efficiency, reduced waste, and avoidance of potential fines or legal issues related to environmental non-compliance. Additionally, many governments offer incentives or tax breaks for implementing environmental protection measures, which can help offset the initial investment.
When planning a 20t/h complete feed mill plant, it is essential to collaborate with environmental experts and local regulatory authorities to ensure all necessary environmental protection measures are properly implemented. This approach not only ensures compliance but also positions the plant for sustainable, long-term operation in an increasingly environmentally conscious market.
For details please contact: pellet making machine
WhatsApp:86 138 3838 9622
Email:enquiry@richipelletmachine.com