A ring die pellet mill is an industrial machine designed for the production of biomass pellets from various raw materials like sawdust, agricultural by-products, and other forms of biomass. Fundamentally, it consists of a key component – the ring die.
The ring die is a cylindrical metal apparatus with numerous small holes uniformly distributed across its surface. As the core element of the pelletizing process, the ring die shapes the material into pellets with consistency and precision.
The design of a ring die pellet mill is both intricate and efficient. It encompasses several vital components, including the main motor, feeder, conditioner, gearbox, rollers, and, of course, the ring die itself.
The feeder introduces raw material into the conditioner, where it is mixed with steam to improve pellet quality and binding. The material is then forcibly pushed through the holes in the ring die by the rollers, resulting in the extrusion of uniformly sized pellets on the outer perimeter of the die.
In general terms, pellet mills operate by compressing raw material into dense and cylindrical shapes known as pellets. The distinctive efficiency of ring die pellet mills lies in their superior ability to handle high volumes and produce durable, premium-quality pellets.
Compared to flat die mills, which use a flat die and operate with a simpler design suitable for small-scale production, ring die pellet machines are tailored for large-scale, continuous operation. This distinction makes them a preferred choice in industrial settings such as biomass energy plants, large farms, and commercial pellet production facilities.
By integrating technical precision with robust construction, ring die pellet mills exhibit formidable performance and longevity. This design sophistication not only extends their operational lifespan but also ensures optimal productivity, making them a valuable asset in the pellet industry.
The structure and mechanics of ring die pellet machines underscore their central role in transforming raw biomass into high-caliber pellets efficiently and consistently.
Benefits of a Ring Die Pellet Mill
1. **Higher Production Efficiency**: Ring die pellet mills are renowned for their superior production efficiency. Their design allows for continuous operation, reducing downtime and maximizing output. The ring shape facilitates the even distribution of raw materials, ensuring a stable and efficient pelletization process.
2. **Consistent Pellet Quality**: One significant advantage of ring die pellet machines is their ability to produce uniform and high-quality pellets. The die’s structure ensures that pellets are evenly compacted, resulting in a consistent density and size, which is crucial for maintaining product standards.
3. **Lower Energy Consumption**: Compared to flat die alternatives, ring die pellet mills generally consume less energy. The power efficiency stems from reduced friction and an optimized processing mechanism, which translates to lower operational costs and a smaller carbon footprint.
4. **Durable and Robust Design**: Ring die pellet machines are built to endure heavy usage. Their robust construction allows them to handle high pressure and abrasive materials, making them ideal for long-term industrial applications. This durability minimizes the need for frequent repairs and replacements.
5. **Lower Operating Costs**: The efficient operation and durable components of a ring die pellet mill contribute to lower overall operating costs. By reducing maintenance needs and energy expenditures, businesses can achieve significant cost savings over time.
6. **Ease of Maintenance**: Although robust, ring die pellet mills are designed for easy maintenance. The accessibility of their components and straightforward mechanical setup ensure that routine maintenance tasks can be performed efficiently, prolonging the machine’s lifespan.
7. **Suitability for Mass Production**: Thanks to their efficiency and high throughput capacity, ring die pellet machines are particularly suited for mass production. They can handle large volumes of materials, making them the equipment of choice for industries requiring continuous, high-quality pellet production.
8. **Versatility in Processing Different Types of Materials**: Whether it’s wood, feed, or biomass, a ring die pellet mill can process a wide range of raw materials. This versatility means that one machine can meet various production needs, enhancing its value and application scope in different industrial sectors.
Why Should I Choose a Ring Die Pellet Mill?
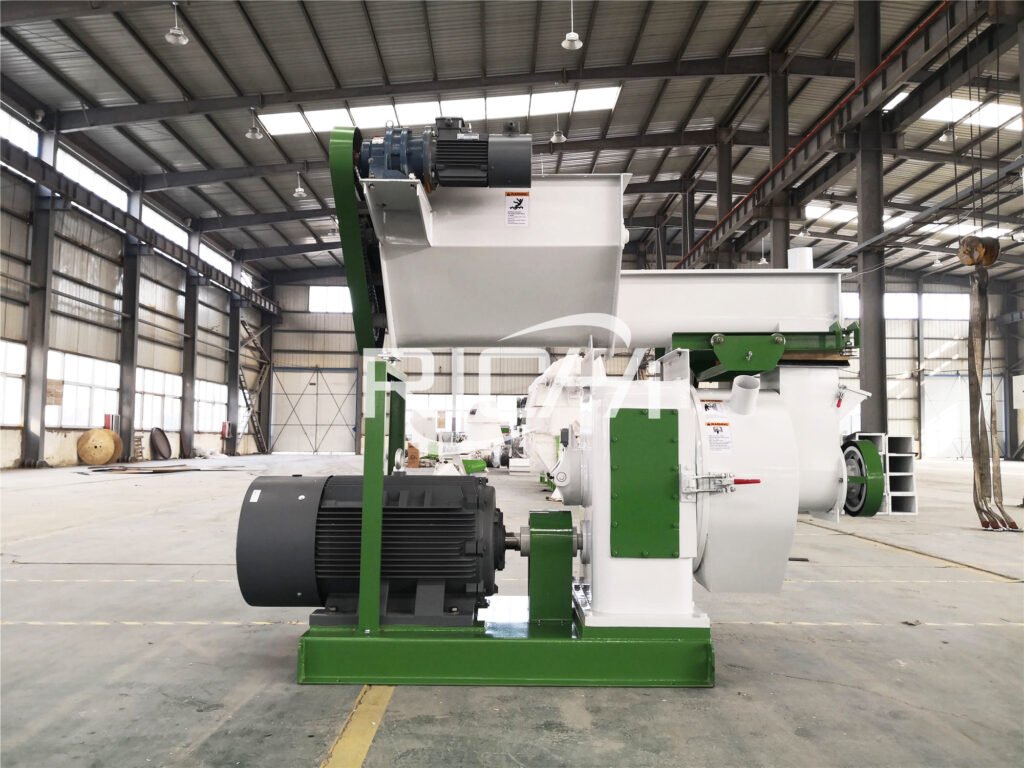
1. Reliability and Durability: One of the primary reasons to select a ring die pellet machine is its exceptional reliability and durability. The robust design and high-quality materials used in manufacturing ensure that these machines can withstand the rigors of continuous operation, minimizing breakdown risk and maintenance requirements.
2. High Throughput Capacity: Ring die pellet mills are renowned for their impressive throughput capacity. Capable of processing large volumes of raw materials efficiently, they are an ideal solution for industries requiring mass production of pellets, thus meeting the demands of heavy-duty operations.
3. Better Heat Distribution: These machines excel in evenly distributing heat during the pelletizing process. This ensures that the raw materials are uniformly processed, leading to higher quality pellets with consistent dimensions, density, and moisture content.
4. Adaptability for a Wide Range of Raw Materials: A significant advantage of using a ring die pellet machine is its ability to process a variety of raw materials. Whether it is wood, biomass, feed, or other organic materials, the versatility of these machines makes them suitable for numerous applications.
5. Efficient Processing: Efficiency is a hallmark of ring die pellet mills. They are designed to convert raw materials into pellets quickly and efficiently, reducing energy consumption and processing time. This leads to increased productivity and cost savings.
6. Cost-Efficiency Over Time: While the initial investment in a ring die pellet machine may be higher compared to other types, the long-term cost benefits are substantial. The machine’s durability, coupled with its low maintenance costs and high efficiency, ensures a favorable return on investment.
7. Advanced Technological Features: Modern ring die pellet mills come equipped with advanced technological features such as automation systems, error detection, and user-friendly controls. These features enhance operational efficiency and simplify the process, making them a preferred choice for advanced industrial applications.
8. Positive Return on Investment: Ultimately, investing in a ring die pellet mill promises a positive return on investment. The combination of high efficiency, durability, adaptability, and reduced operational costs ensures that businesses can maximize their profits while maintaining high-quality production standards.
Working Principle of a Ring Die Pellet Mill
Understanding the working principle of a ring die pellet mill is crucial for optimizing its performance and ensuring the quality of the finished pellets. Below, we provide a step-by-step explanation of how a ring die pellet machine operates, detailing each stage of the process from the initial feedstock preparation to the final product packaging.
1. Feedstock Preparation
The process begins with the preparation of the raw materials, often consisting of various biomass sources such as wood, agricultural residues, or grasses. The feedstock needs to be cleaned and reduced to an appropriate size, which generally involves chipping, grinding, or milling.
Ensuring the consistency and moisture content of the feedstock is vital as these variables significantly impact the efficiency of the ring die pellet mill.
2. Material Feeding into the Pellet Mill
Once the feedstock is prepared, it is delivered into the pellet mill’s feeding system, typically via conveyors or augers. The material is then directed into the conditioning chamber where it is mixed with steam to soften the fibers. This conditioning phase enhances the binding properties of the biomass, making it easier to compress.
3. Compression of the Material through the Ring Die
In the core part of the machine, the conditioned material is pressed against a rotating ring die. Rollers within the ring die pellet mill push the feedstock through the die holes, exerting high pressure which compresses and shapes the material into pellet form. The unique cylindrical design of the ring die allows for high throughput and uniform pellet size.
4. Pellet Formation
As the material is forced through the die holes, it forms dense and solid pellets. The configuration of the ring die and the operational parameters, such as pressure and temperature, play significant roles in determining the physical properties and durability of the pellets produced by the ring die pellet machine.
5. Pellet Cooling
The freshly extruded pellets are hot and somewhat pliable, necessitating a cooling phase to harden and stabilize them. A cooling system, often involving air blowers or cyclones, is employed to reduce the pellet temperature and moisture content, preparing them for handling and storage.
6. Final Product Packaging
The final stage involves the packaging of the cooled pellets. Depending on the intended market, pellets are usually packed in bags, bulk containers, or offered in loose form. Proper packaging ensures the preservation of pellet quality during storage and transportation, facilitating easier distribution to end-users.
Through careful execution of these stages, a ring die pellet mill converts raw biomass into uniformly sized, high-quality pellets, ready for use in various applications such as heating, power generation, or animal feed.
Specific Parameters of a Ring Die Pellet Mill
The efficiency and productivity of a ring die pellet mill largely depend on understanding and selecting the appropriate parameters that meet your operational needs. These parameters encompass size and dimensions, capacity (tons per hour), power requirements, die diameter, roller size, pellet diameter, and the types of materials suitable for processing.
Each of these specifications plays a crucial role in defining the overall performance and suitability of the ring die pellet machine for different applications.
Firstly, considering the size and dimensions of the ring die pellet mill is vital, as it directly influences installation space and operational convenience. Smaller ring die pellet machines are typically suitable for small businesses or individual operators with limited space, while larger units cater to industrial-scale operations requiring higher output.
Capacity, generally measured in tons per hour, is another critical parameter. Small-scale operations might find a capacity of 0.5-1 tons per hour adequate, whereas large-scale industries often require machines capable of producing 5-10 tons per hour or more, ensuring productivity aligns with market demand and business scale.
Power requirements vary depending on the machine size and intended use. Smaller machines may operate efficiently on 22-45 kW, whereas industrial machines might need up to 200 kW or more to handle large volumes continuously. Selecting a ring die pellet mill that matches your available power supply ensures seamless operations.
The die diameter and roller size significantly influence the pelletizing process. Die diameters can range from 300 mm to over 700 mm, with larger diameters suitable for large-scale production. Similarly, roller sizes should correspond to die dimensions for optimal compression and pellet formation.
Pellet diameter, typically ranging from 4 mm to 12 mm, determines the end-use of the pellets. Smaller diameters are often used for animal feed, while larger diameters may be more suitable for biomass fuel applications. Choosing the correct pellet size is crucial for meeting specific industry standards and customer requirements.
Lastly, the type of material the ring die pellet machine can process is essential. While pellet mills can handle a variety of materials such as sawdust, straw, biomass, and feed, choosing a machine tailored to the specific material ensures efficiency and durability.
Understanding these parameters helps in selecting the right ring die pellet mill, whether for a small business seeking efficiency or a large-scale industry aiming for high output. By matching the machine’s specifications to your specific operational needs, you can optimize productivity, minimize downtime, and ensure long-term reliable performance.
Advantages of Choosing Richi Machinery as Your Supplier
When it comes to selecting a supplier for ring die pellet mills, Richi Machinery presents several advantages that set them apart from other manufacturers. Below is a detailed list of benefits that you can expect when choosing Richi Machinery:
1. Extensive Industry Experience: Richi Machinery boasts over two decades of expertise in the pellet mill industry. Their extensive knowledge and experience ensure that they can provide trustworthy and innovative solutions tailored to meet the needs of various applications.
2. Comprehensive Product Range: One of Richi Machinery’s key strengths is their expansive product portfolio. They offer a wide variety of ring die pellet machines, catering to different materials and output capacities. This versatility allows clients to find the perfect machinery for their specific requirements.
3. Stringent Quality Assurance: At Richi Machinery, quality is paramount. Their robust quality assurance measures ensure that each ring die pellet mill undergoes rigorous testing and inspection. This guarantees high performance, durability, and reliability, giving customers peace of mind.
4. Advanced Technology: Richi Machinery is at the forefront of technological advancements in pellet milling. They continuously invest in research and development to integrate cutting-edge technologies into their products. This commitment results in more efficient, energy-saving, and cost-effective pellet machines.
5. Exceptional Customer Service: Customer satisfaction is a cornerstone of Richi Machinery’s business philosophy. They offer prompt and responsive customer service, addressing queries and concerns efficiently. Their dedicated support team strives to provide a seamless and satisfactory client experience.
6. Competitive Pricing: Richi Machinery offers high-quality ring die pellet mills at competitive prices. Their cost-effective solutions make advanced pellet milling technology accessible to a broader range of industries, providing excellent value for investment.
7. Customization Options: Recognizing the unique needs of different applications, Richi Machinery offers customization options for their ring die pellet machines. Clients can request personalized features and specifications, ensuring that the equipment perfectly aligns with their operational requirements.
8. Robust After-Sales Support: Richi Machinery’s commitment to customers does not end after a sale. They offer strong after-sales support, including maintenance services, technical assistance, and spare parts availability. This ongoing support helps clients achieve optimal performance and longevity from their equipment.
FAQs about Ring Die Pellet Mills
When considering the adoption of a ring die pellet mill, prospective users often have numerous questions regarding the functionality and practical aspects of these machines. Below, we address some of the most common inquiries:
What materials can be processed by a ring die pellet machine?
Ring die pellet machines are versatile and capable of processing a wide array of materials. These include but are not limited to, wood, biomass, feedstock, and agricultural residues like straw and rice husk. The adaptability of a ring die pellet mill ensures efficient pelletization of different raw materials, which is suitable for various industrial and commercial applications.
How does maintenance work for a ring die pellet mill?
Maintenance is a crucial aspect to ensure the longevity and efficient operation of a ring die pellet machine. Routine checks should include inspecting the die and roller for wear and tear, ensuring the lubrication system is functioning properly, and cleaning the equipment regularly to avoid blockages. Periodic professional servicing can also help in identifying potential issues before they lead to significant downtimes.
What are the operational costs associated with ring die pellet mills?
The operational costs of running a ring die pellet mill include energy consumption, labor, raw material procurement, and maintenance. While these costs can vary depending on the scale of operation and the specific machine model, opting for a high-quality ring die pellet mill can enhance production efficiency and reduce long-term expenses.
What safety features are included with ring die pellet machines?
Modern ring die pellet machines are equipped with several safety features to ensure safe operation. These often include emergency stop buttons, overload protection systems, and automatic shut-off mechanisms to prevent accidents during operation.
Additionally, proper training and adherence to safety guidelines are crucial to maintaining a safe working environment.
Addressing these FAQs provides a clear understanding of how ring die pellet mills operate and what potential users can expect in terms of versatility, maintenance, operational costs, and safety features. With this knowledge, businesses can make well-informed decisions when selecting the appropriate ring die pellet machine for their needs.
Final Thoughts on Ring Die Pellet Mills
Throughout this comprehensive examination of ring die pellet mills, we have underscored the pivotal benefits and characteristics that make them an indispensable asset in the biomass processing industry.
The ring die pellet machine stands out due to its efficiency, durability, and the ability to produce high-quality pellets. Unlike flat die pellet mills, the ring die configuration ensures a more consistent feed production, less wear on mechanical components, and greater energy efficiency.
Key advantages, such as enhanced pellet quality, lower processing costs, and reduced maintenance requirements, position ring die pellet mills as the preferred choice for many businesses.
Moreover, their capacity to handle various raw materials, including sawdust, straw, and agricultural residues, adds to their versatility and appeal. This makes them particularly valuable for enterprises aiming to optimize their biomass processing operations and improve overall productivity.
Potential customers should consider ring die pellet mills for their superior performance and economic benefits. The technological advancements integrated into these machines provide significant improvements over traditional pellet mills.
They are designed to achieve higher throughput rates, maintain consistency in pellet size and composition, and minimize downtime, thereby boosting operational efficiency and profitability.
When selecting a supplier, Richi Machinery emerges as a reliable partner due to their commitment to quality, innovation, and customer satisfaction. Richi Machinery’s extensive experience and dedication to providing state-of-the-art ring die pellet mills ensure that clients receive products that meet stringent industry standards.
Their comprehensive customer support and expert guidance further enhance the value proposition, making Richi Machinery a prudent choice for businesses looking to invest in top-tier pelletizing technology.
Ultimately, ring die pellet mills represent an intelligent investment for businesses aiming to leverage advanced engineering for superior pellet production. By choosing a trusted supplier like Richi Machinery, companies can rest assured that they are equipping themselves with machines designed for optimum performance, sustainability, and long-term success.